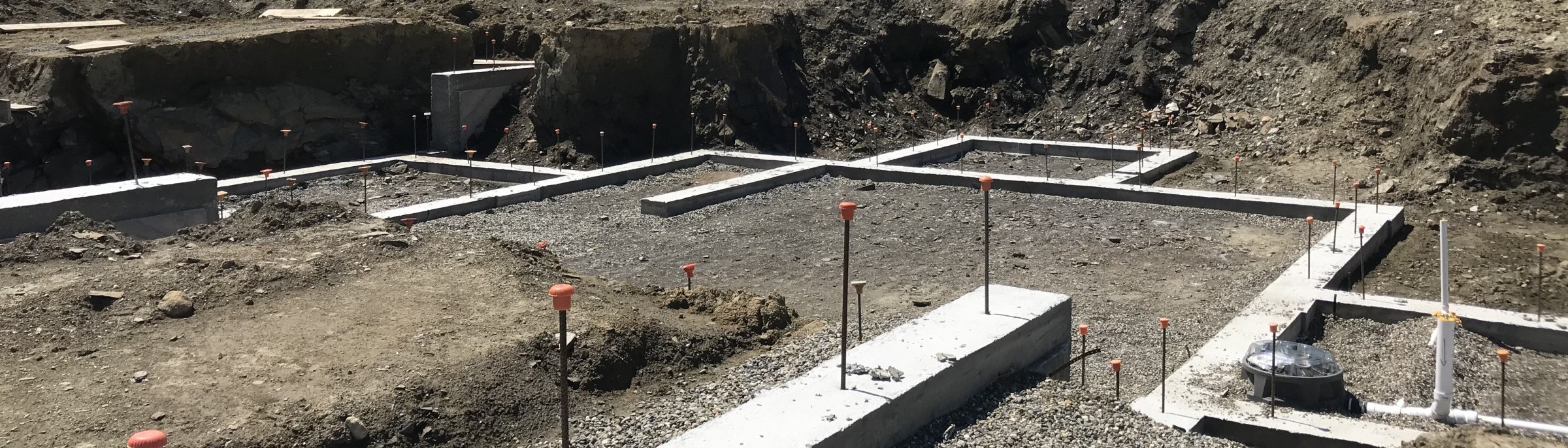
The Anatomy of a New Home Build: Part 2 - Moving Rocks and Dirt
Preparing Your land and foundation
This home is sited on a large piece of land and the house site has an incredible view of the Worcester Range to the west. The house site sits back from the road almost 900'. The terrain is relatively flat and is a wide-open meadow which helps, but it does contribute significantly to the cost of the overall home build. The driveway is about 1100' long and not only does a quality driveway need to be constructed, but power and communication wires must also be brought in. That takes considerable coordination with the telephone, cable, and power companies to place those properly - a process that started when there was still snow on the field.
Laying out the Driveway and Power
Burying power from the main road to avoid seeing poles and wires was an option but the length and expense made it prohibitive. The next best option was to tuck the bulk of that utility up against a tree line until within 200' of the home. Coordinating with the power company, we helped place the poles so as to avoid cutting trees and allowed us to site the driveway along side them. None of the views will be interrupted by wires and that process takes considerable effort because power companies are generally more interested in protecting their lines than view aesthetics. The telephone and cable lines will also follow the same path on the poles.
Once at the last pole, all utilities will go underground and serve the home and its propane backup generator on a remote meter panel. Being well away from any community water or sewer source, the home will have a drilled well and septic system.
Ledge and How to Handle It
Working with our excavation contractor, Gene and Donny from Gene Bowen Excavating in Calais, VT, we laid out the road and utilities and began construction in mid June. First was to build the driveway and strip topsoil from the house site to be stored for later use during final grading. We also knew we would likely hit ledge based on the results from our test digging in the fall.
Only the central core of the home has a full basement so that was the critical area we needed to get down 8' or so into the ground. Our initial digging revealed some ledge - thankfully not too much of it - and it only required we slightly shift the home's position to avoid unnecessary work. It also required we hire a specialty contractor, Northern Rock Services from New Haven, VT, to come in and tune up the cellar hole with his specialty ledge hammering equipment.
We have worked closely with Colby, Northern Rock's owner, on multiple projects and have found his expertise in removing rock invaluable. More economical and less disruptive than blasting, Colby has provided the solution to all sorts of rock problems and is very cost effective. We needed him for just one day with his smaller machine to tune up a few corners of the foundation and get an area of the floor down about a foot to get a full height basement in.
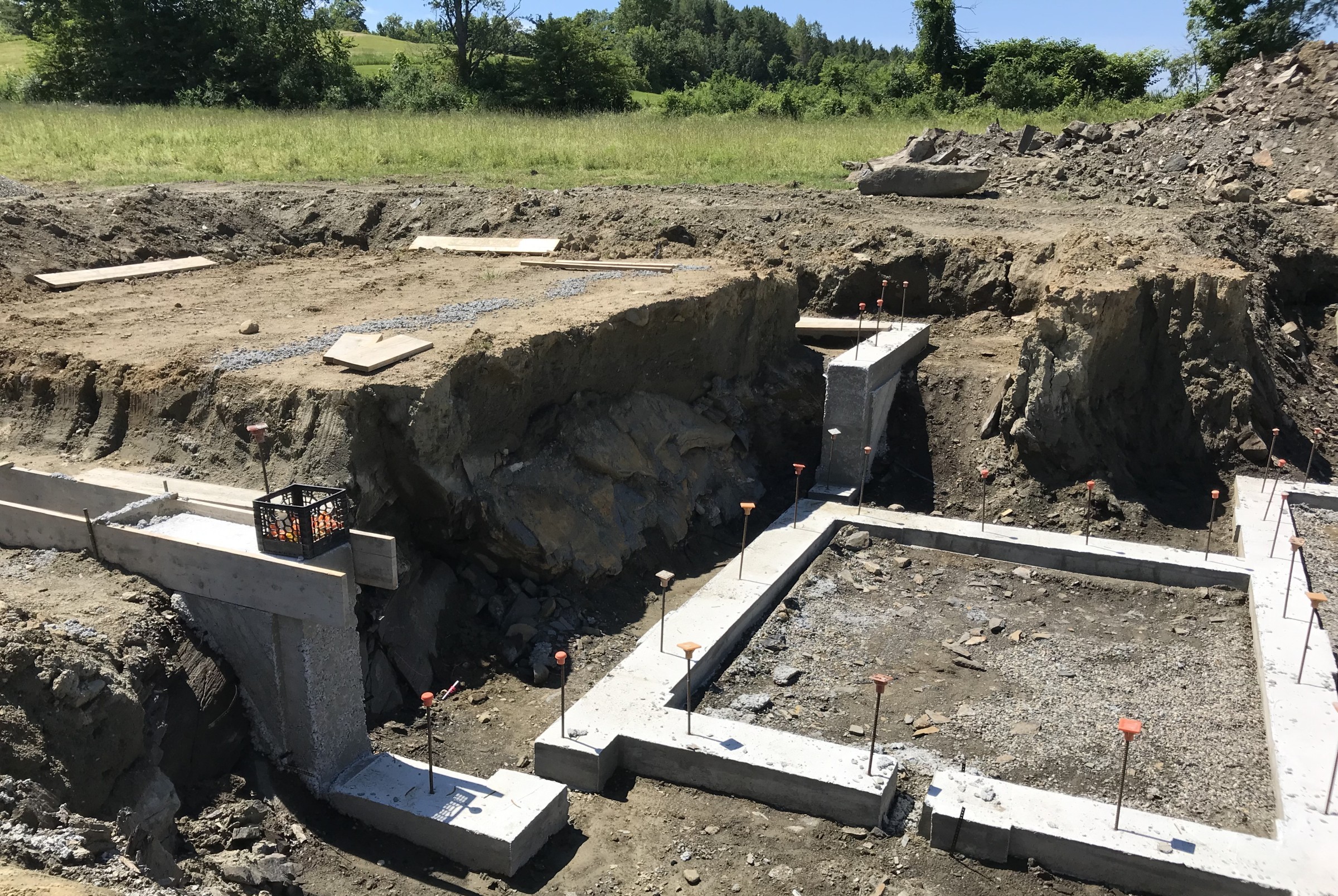
Footings are the First Step
The next step once the hole was dug was to begin pouring the foundation. That starts with laying out the footings which we did with our concrete contractor, Hutch Concrete on beautiful late June day. This home has a complicated foundation and Gene and Donny did a nice job of working closely with us and Hutch to fine-tune a few spots for the footings. It is important to work with a concrete contractor that has the right tools for a project like this. Employing tools like a "Total Station" is critical to getting square and accurate foundations when there are lots of corners.
These total stations can cost upwards of $10,000 and are an investment in producing quality work. We have worked with Hutch for 12 years now and are confident in their process and results. It is critical from our perspective to have accurate concrete because we utilize a prefabrication process of our wall panels, floor systems and roof trusses which happens concurrently with the concrete. Neither can be changed easily after the fact, so triple checking things to make sure we get them correct the first time is part of our process. Everything was poured in time for the 4th of July holiday weekend and all ready to form the walls the week after.