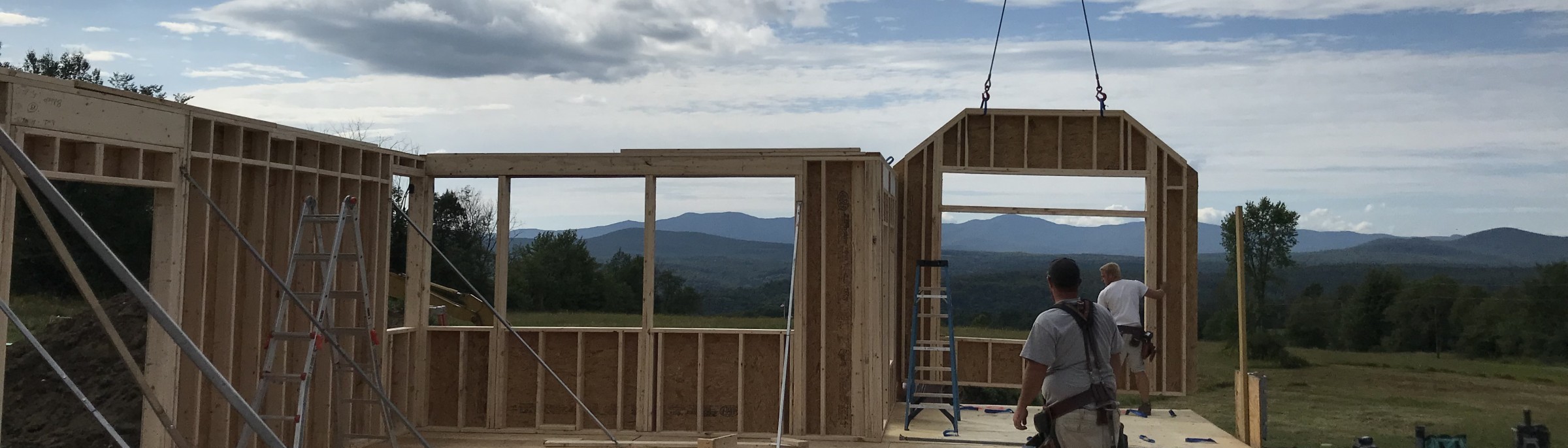
The Anatomy of a New Home Build: Part 3 - Framing With a Crane
framing your vermont home
Allied has been using pre-fabrication of its building components for almost 10 years now. There is a learning curve and some potential pitfalls, but once we worked out the kinks long ago, we now utilize the prefabrication process to increase speed, quality and reduce cost. We have worked with several prefabrication companies over the years and now work with UsiHome out of Magog Quebec.
We have now done 4 buildings with them and have found them easy to work with, reasonably priced, and deliver a level of quality from the factory we are comfortable with. This process prefabricates all the wall panels, roof trusses, and floor system pieces and allows us to cut the framing process by about a factor of 10 - valuable days in our short building season. It is different from "modular" construction which delivers mostly finished boxes to the site. With prefabrication, we finish the process with the shell of the building.
Speed: A crew of 4 people erected this house with a crane in 3 full days. Normally, a house this size would have taken closer to 3-4 weeks to reach the same level with the same sized crew framing it on site. Since good carpenters are hard to find in Vermont these days, not only is it faster, it's a smarter way of accomplishing this phase of construction. It is also safer to frame a building this way. All the heavy lifting is done with a crane, and so there is far less chance of a carpenter being injured trying to lift something, falling while carrying something heavy, or having something fall on them. It is a lot easier on their bodies which is also a consideration with our aging carpenter pool in Vermont.
Price: The efficiency of framing materials in a factory and the factory purchasing materials in large volumes creates a level of cost efficiency that can't be competed with framing on site. While this does reduce the number of materials we purchase from our local supplier, a dynamic we are cognizant of, in the grand scheme of things it is a relatively small portion of the total materials and we source the remainder locally when possible to support our local community. In the best of circumstances, the cost might be comparable, but the bigger the project gets the more the scales tip towards prefabrication being less expensive.
Quality: Given enough time, our crew could frame a home perfectly within an eighth of an inch or less everywhere. But that takes time, and Vermont is notorious for bad weather all year round. When framing by hand on-site, a home's framing members are often exposed to at least half a dozen rain cycles before drying in, and often times a lot more. This can affect the quality and the time it takes for the craftsmen to adjust for that reduced material quality and at worst permanent damage to the materials. When a home is prefabricated, it is built in a controlled environment in a factory.
Parts are measured by a computer and assembled by workers on jig tables. Trusses are also built in the same place and are produced to the 16th of an inch. If you catch the right weather window, your home can be dried in, never having been rained on. Even in bad weather, it encounters far fewer of these rain events and it helps maintain the quality. While there are some inevitable adjustments that have to be made in the field, the amount of time to do that is far outweighed by the time savings and UsiHome has been very good about discounting for errors we have had to fix in the field. In the end, everyone wins with this process.
Working with Dom Guerrina and his crew form Guerrina Crane, was a pleasure and the three tractor-trailer loads of walls, floors, and roof trusses went in and after a full week of work, the roof was more or less dried in.